Listen to the article
Getting your Trinity Audio player ready...
|
In the world of industrial maintenance, it is common to find a large number of abbreviations and acronyms that can be confusing to those unfamiliar with the subject. However, it is important to understand what these abbreviations mean and how they are used in the context of maintenance. It is important to know maintenance abbreviations and acronyms because they are frequently used in technical documentation, manuals and maintenance reports. Knowing them allows technicians and other maintenance professionals to communicate more effectively and better understand the technical information they are using. In this article, we will explore some of the most common and up-to-date abbreviations and acronyms used in industrial maintenance.
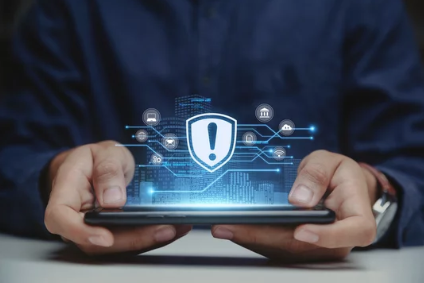
Common maintenance abbreviations
Some of the more common abbreviations used in industrial maintenance include:
PM: Preventive Maintenance. Preventive maintenance is a technique used to keep equipment in good working order by performing periodic inspections and minor repairs before failure occurs.
CM: Corrective Maintenance. Set of reactive tasks, based on replacing, performing interventions or repairing when an asset ceases to perform its function or clear symptoms of deterioration are known. It can be programmed or to attend unplanned failures.
CBM: Condition Based Maintenance. It is a maintenance strategy that integrates IoT technology with assets, which through highly specialized software measures the condition of equipment, through variables that indicate the status of a part or component, in order to take appropriate inspection or intervention actions before a functional failure occurs.
CMMS: Computerized Maintenance Management System. CMMS is software used to help companies manage their maintenance and asset tracking programs.
PdM: Predictive Maintenance. Predictive maintenance uses monitoring and data analysis to predict when equipment failure will occur so that action can be taken to prevent it.
RCA: Root Cause Analysis. RCA is a technique used to identify the root cause of a problem, allowing technicians to solve the problem more effectively.
TPM: Total Productive Maintenance. TPM is a maintenance management philosophy that focuses on involving all employees to improve equipment efficiency and reduce downtime.
FMEA: Failure Mode and Effect Analysis. FMEA is a technique used to analyze the possible failure modes of a system and evaluate their impact on performance.
FMECA: Failure Mode, Effects and Criticality Analysis. It builds on the FMEA analysis, adding a risk rating to each of the failure modes by means of the Risk Priority Index (RPN).
RPN: Risk Priority Number. It consists of the index that is calculated as the product between the severity rating, the probability of occurrence and the ease of detection. It is used in the FMECA analysis to obtain a criticality rating for each failure mode in the assets.
RCM: Reliability Centered Maintenance. RCM is a systematic approach used to determine the best maintenance strategy for a specific piece of equipment or system.
RBI: Risk Based Inspection. It is a methodology used to define and decide the most appropriate way to perform inspections of equipment and assets by technical personnel. It establishes the strategy based on risk principles, so that efforts are oriented towards high-risk equipment with high potential for equipment failure.
FTA: Fault Tree Analysis. Analysis method used to identify the causes of an event or failure, making a “map” or tree of causes at different levels.
PMO: Preventive Maintenance Optimization. It is the process used to optimize the results of existing maintenance plans through methodologies such as SAMPLEX. Regardless of how it has been defined, its objective is to reduce the technical workload of maintenance tasks in terms of resource consumption and labor usage.
MSG: Maintenance Management Groups. This is a concept designed in the 1960s by the North American Civil Aeronautics (FAA) in response to the use of maintenance methodologies that were considered too costly and dangerous. The process sought to re-evaluate and reorient management to maintain aircraft functions, and to identify the different ways to fail.
EM: Emergency Maintenance. This type of maintenance is performed when an unexpected equipment failure occurs and requires an immediate response. The objective is to solve the problem as quickly as possible to minimize damages, production costs and/or avoid complaints, problems in the services provided.
EAM: Enterprise Asset Management. EAM is a holistic approach to enterprise asset management that includes maintenance planning, scheduling and execution. EAM is used to manage enterprise assets, improve the efficiency of the production process and extend the life of equipment.
Common maintenance acronyms
In addition to the above abbreviations, there are some common acronyms used in industrial maintenance, such as:
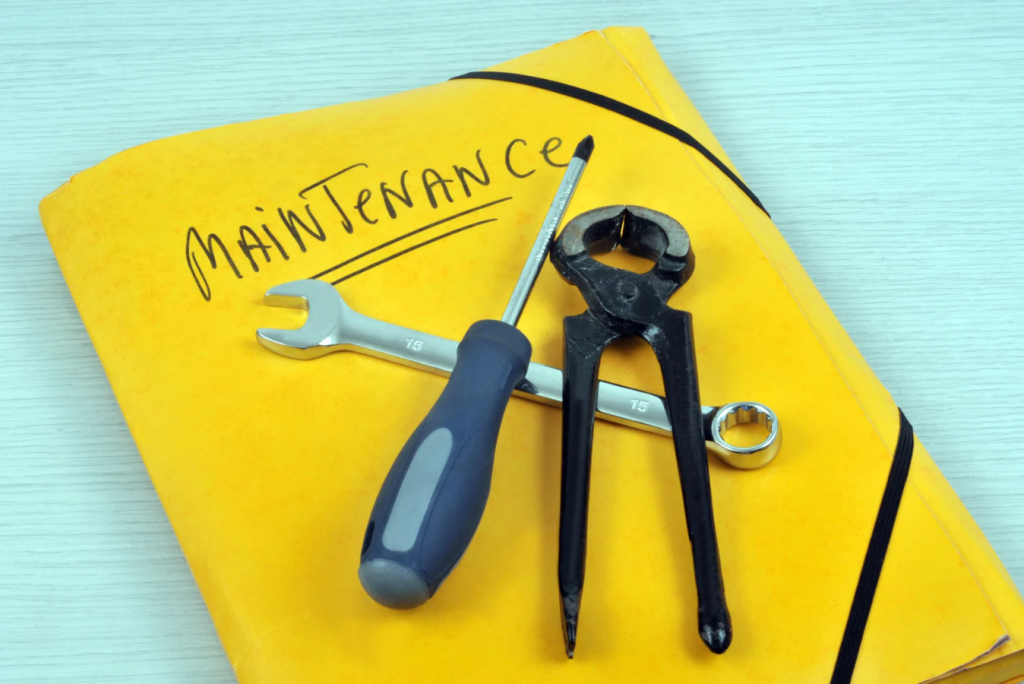
HVAC: Heating, Ventilation and Air Conditioning. HVAC refers to the system that controls the indoor climate of a building.
EMS: Energy Management System. EMS is a system used to control and manage energy consumption in a building or system.
PLC: Programmable Logic Controller. The PLC is a device used to control and automate industrial processes.
SCADA: Supervisory Control and Data Acquisition System. SCADA is a system used to monitor and control industrial processes.
HMI: Human User Interface. The HMI is a screen or panel used to display information and allow users to control equipment or systems.
MTBF: Mean Time Between Failures. An indicator of the reliability of an equipment or system that is used to determine the appropriate frequency of preventive maintenance.
MTTR: Mean Time To Repair. An indicator of the average time required to repair an equipment or system after a failure.
OEE: Overall Equipment Effectiveness. OEE is a measure of equipment efficiency and is used to evaluate the productivity of equipment in a production process. It is calculated by multiplying the percentage of availability, the percentage of throughput and the percentage of quality.
Best practices in the use of abbreviations and acronyms.
It is important to follow some best practices to ensure that abbreviations and acronyms are used effectively in industrial maintenance. Below are some recommendations:
- Avoid excessive use of abbreviations and acronyms. Sometimes abbreviations and acronyms can create confusion rather than clarify information. Therefore, it is important to use them only when necessary and make sure that the audience understands them.
- Define abbreviations and acronyms at the beginning of a document or in a glossary section. This helps the audience understand the abbreviations and acronyms used in the document in question. While using abbreviations and acronyms can save time and space, it is important to consider the audience. If the audience is not familiar with the abbreviations and acronyms used, it can cause confusion and misunderstanding. Therefore, it is important to use them only when necessary and to define them clearly for the audience.
- Use abbreviations and acronyms consistently. It is important to use the same abbreviation or acronym throughout the document to avoid confusion.
- Ensure that abbreviations and acronyms are accurate and up-to-date. Abbreviations and acronyms can change over time, so it is important to verify that the abbreviations and acronyms used are accurate and up to date, it is important to verify the abbreviations and acronyms you use in your maintenance documentation with reliable sources, such as maintenance manuals, technical guides, and industrial maintenance organization websites.
- Common abbreviations and acronyms in industrial maintenance can be found in maintenance manuals, technical guides and other industrial maintenance-related documents. You can also find information online through search engine searches.
New maintenance techniques abbreviations.
There are new maintenance techniques that are emerging thanks to the advance of technology and that can be very useful in the future. Here we describe some of them:
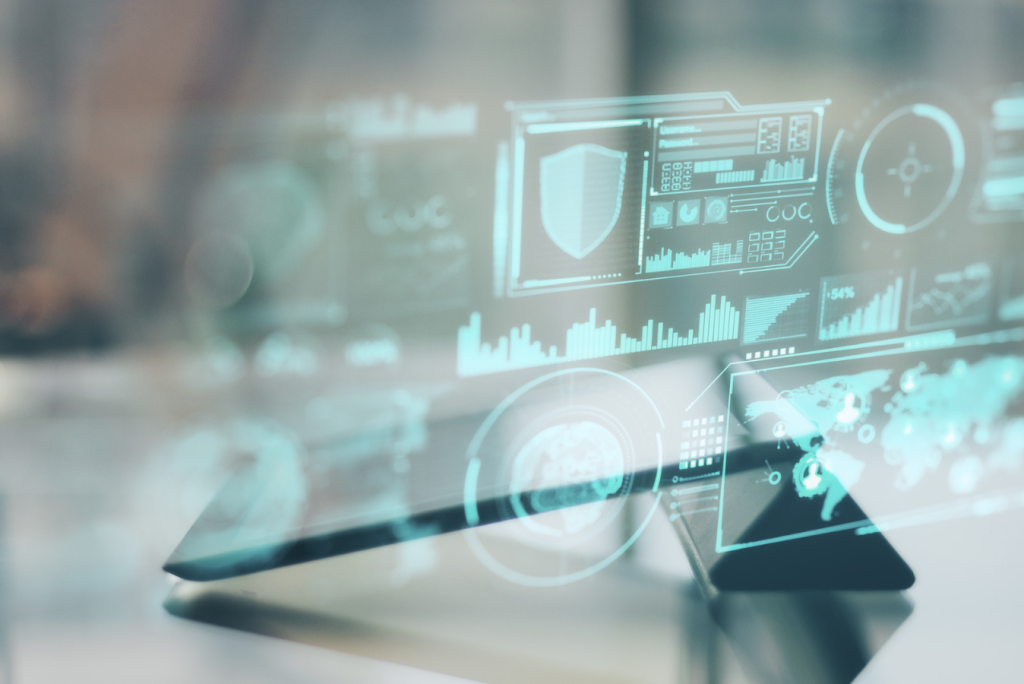
VRM: Virtual Maintenance. This technique uses virtual reality technology to train maintenance technicians and improve their ability to repair equipment more effectively. Technicians can practice different maintenance scenarios in a virtual environment before applying them in the real world, which can help reduce errors and downtime.
IoTPdM: Predictive maintenance based on the Internet of Things (IoT). Internet of Things (IoT) technology enables the connection of sensors and devices over the internet, allowing real-time data collection and analysis. In IoT-based predictive maintenance, sensors are used to monitor equipment performance and detect potential failures before they occur. This allows companies to take preventive measures to avoid unplanned downtime and reduce maintenance costs.
CoM: Collaborative Maintenance. Collaboration between maintenance teams can improve efficiency and quality of work. Real-time communication technology, such as video conferencing, can be used to enable maintenance technicians in different locations to collaborate and solve problems together. In addition, augmented reality technology can also be used to allow experienced technicians at one location to guide and supervise technicians at another location.
DABM: Data analytics-based maintenance. Data analytics can be used to identify patterns and trends in maintenance data. By using data analytics techniques, companies can identify recurring problems and determine the underlying causes. This allows companies to take preventative measures to avoid failures in the future.
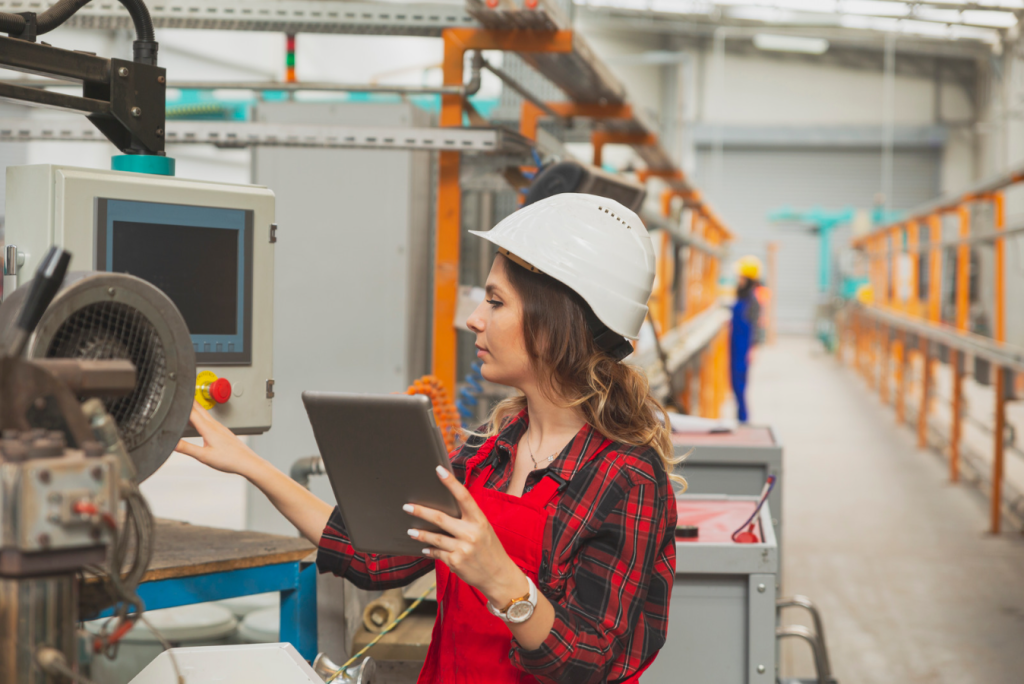
AM: Autonomous Maintenance. This technique involves the use of robots and artificial intelligence systems to perform maintenance tasks automatically. Robots can perform repetitive or dangerous tasks, while artificial intelligence can help predict failures and plan maintenance before a failure occurs.
RTM: Real Time Maintenance. This technique uses sensors and data analysis systems to provide real-time information on the condition of equipment. Maintenance technicians can constantly monitor equipment and perform maintenance in a timely manner before failures occur.
BBM: Blockchain-Based Maintenance. This technique uses blockchain technology to improve transparency and efficiency in managing company assets. The blockchain can record the entire maintenance history of a piece of equipment, including past repairs, parts replaced and associated costs. This can help simplify asset management and improve decision making.
We hope this article has been helpful, if you would like to learn more about CMMShere, contact us here, or leave your information in the chatbot on our site so that a representative from our company can contact you as soon as possible.
No comment yet, add your voice below!