Vilfredo Pareto fue ingeniero, sociólogo, economista y filosofo, nacido en Paris el 15 de Julio de 1848, estableció el principio de Pareto también conocido como la regla 80/20 y ley de los pocos vitales, mediante este principio explica estadísticamente que en cualquier conjunto poblacional de todo tipo que contribuye a un efecto común, es una proporción pequeña la que contribuye a la mayor parte del efecto.
El nombre de Diagrama de Pareto fue dado por Joseph Juran en honor al economista Pareto, quien realizó un estudio sobre la distribución de la riqueza, en el cual descubrió que la minoría de la población poseía la mayor parte de la riqueza y la mayoría de la población posee a la menor parte de la riqueza. Con esto estableció la llamada “Ley de Pareto” según la cual la desigualdad económica es inevitable en cualquier sociedad.
La aplicación de este principio en las empresas se puede dar en la cadena de valor en la cual el 80% de los procesos en la cadena se logra con el 20% de las actividades, aquí podemos encontrar un ejemplo perfecto, considere toda la riqueza del mundo, un 20% de la población posee el 80% de la riqueza total, de acuerdo al fondo monetario internacional, el producto interno bruto de los 196 países en el mundo en el 2011 fue de US$79 trillones y alrededor de US$63 trillones (80%) son aportados por tan solo 22 países, así que el 80% de la riqueza esta concentrada en solo el 9% de los países del globo.
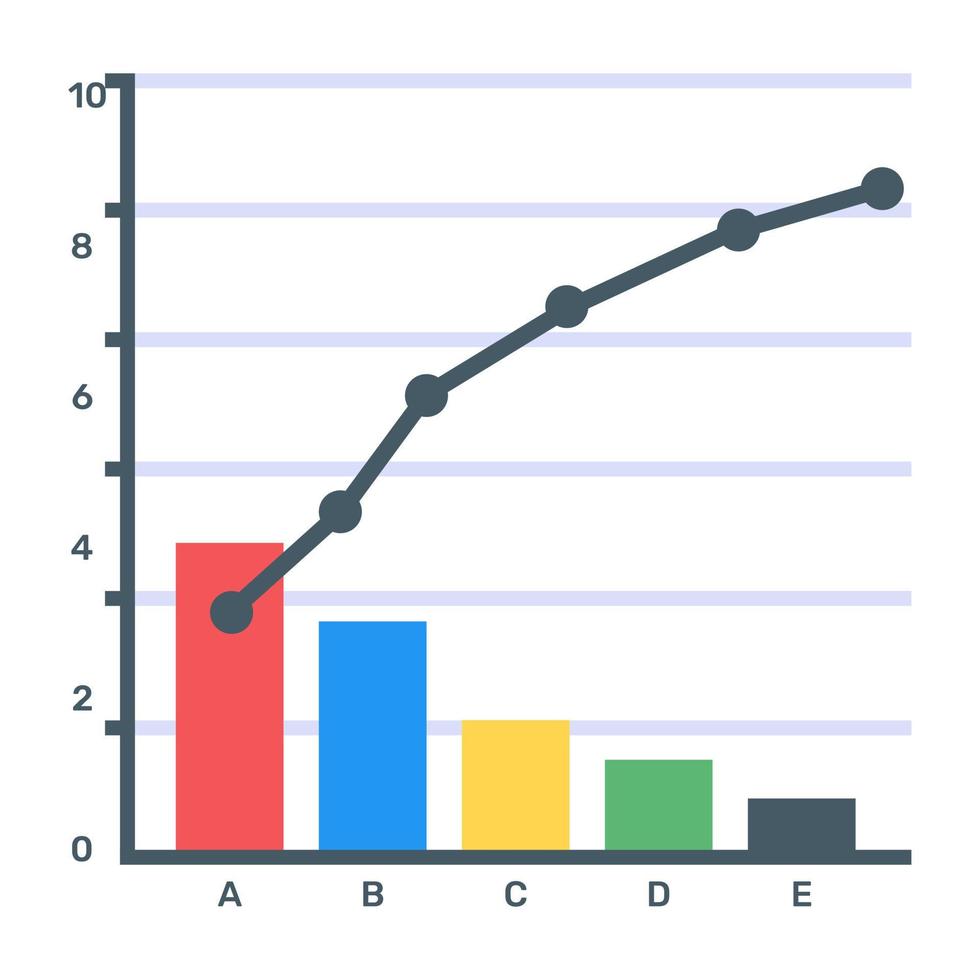
US$15 trillones o el 19% del total de la riqueza es producida por un solo país, Estados Unidos, así que el 19% de la riqueza mundial es producida por el 0,5% de todos los países a nivel mundial (Ref: World Economic Forum, Octubre 2012).
Este principio de 80/20 es una metodología ampliamente utilizada en el RCA (Root Cause Analysis, (para mayor información puede consultar nuestro ebook: CMMShere – Análisis de Causa Raíz en la Gestión de Mantenimiento) para la determinación de los orígenes de los modos de fallas en piezas, sistemas o procesos en los que hay involucrados activos que son susceptibles de mantenimiento correctivo o reparación.
¿Qué es una falla?
Una falla es toda condición que afecta la operación o funcionalidad normal o que se considere estándar de un equipo, máquina o proceso y que es susceptible de mantenimiento correctivo inmediato dependiendo de la clasificación de gravedad del activo dentro del área de proceso.
Existen dos tipos de falla, la falla funcional que es la que impide que un equipo continue en operación y una falla potencial es la que la avería no inhabilita al equipo para siga funcional, pero que en determinado momento bajo las condiciones de operación determinadas puede causar una falla funcional, por ejemplo el ruido excesivo en piezas giratorias que están ligadas a un rodamiento, el equipo puede seguir operando pero es seguro que el rodamiento en cualquier momento fallará causando la salida de operación del activo.
Con el fin de mitigar los eventos causados por fallas en activos y permitir reducir los costos de mantenimiento y disminución de la cantidad de repuestos en inventarios, es primordial realizar los análisis de falla, con el fin de analizar el evento hasta lo más profundo, ya sea en piezas o como un todo del sistema o subsistema al que pertenece el activo, determinar la causa de la falla y a partir de esa causa determinar las acciones correctivas y su implementación, lo que llevará a que la tasa de fallos disminuya a lo largo del tiempo brindando así variados beneficios tanto como para la efectividad del equipo de mantenimiento como para la productividad empresarial.
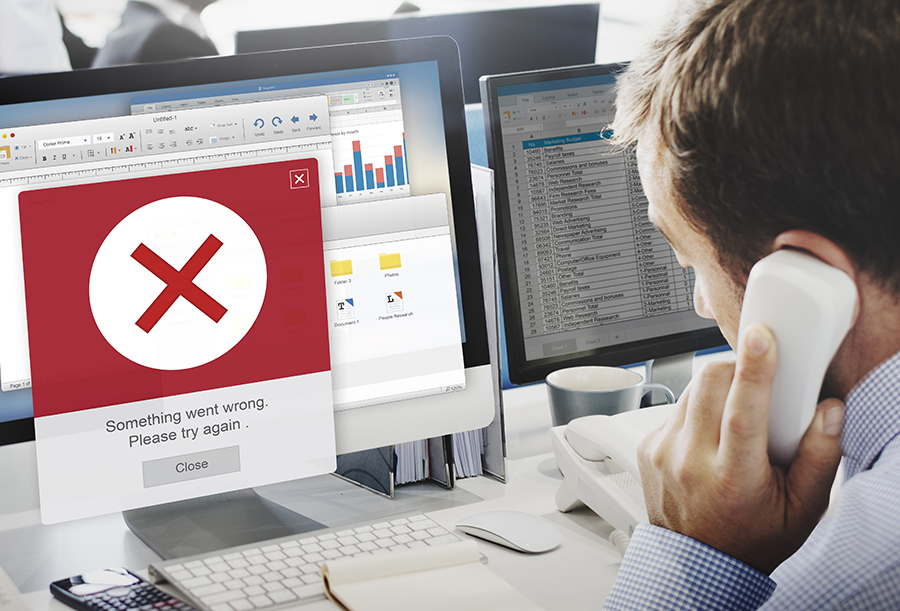
El mantenimiento preventivo permite igualmente disminuir la tasa de fallos, en equipos nuevos funcionara perfectamente este tipo de mantenimiento (para mayor información consulte nuestro ebook: CMMShere – Tipos de Mantenimiento), pero muy seguramente el fabricante llevará al equipo para asegurar su garantía a un sobremantenimiento, a su vez se irá construyendo el historial de mantenimiento y de fallas que permitirá ir enriqueciendo los análisis posteriores de falla para así iniciar una etapa de mantenimiento basado en confiabilidad.
Metodología de Pareto en mantenimiento
La Ley de las Prioridades 80/20 dice: “El 80% de los problemas que ocurren en cualquier actividad son ocasionados por el 20% de los elementos que intervienen en producirlos”. aplicando este principio a la gestión de mantenimiento se cumple, con bastante certeza, que un número reducido de elementos son los responsables de la mayoría de averías de los activos o que un reducido número de activos ocasiona la mayor carga técnica de mantenimiento.
El método de análisis de esta principio es él diagrama ABC y sirve para conseguir el mayor nivel de mejora con el menor esfuerzo posible. Se trata de una representación gráfica de los datos obtenidos sobre un problema, que ayuda a identificar y seleccionar los aspectos prioritarios que hay que tratar.
Cuales son los pasos a seguir para graficar la ley de prioridades:
- Recopilar el histórico de fallas de un equipo, la fuente de la lista de fallas es el CMMShere, este software posee la capacidad de almacenar todos los fallos de un activo y arrojar todos los costos asociados a su reparación como costo de personal, costos de insumos y repuestos y otros costos que pueden ser ejecutados en terceros especializados.
- Diseñar una tabla, en la primera columna anotar las fallas del activo en orden decreciente de sus costos asociados.
- En la segunda columna calcular y anotar el porcentaje relativo o peso relativo de los costos presentados en cada caso.
- En la tercera columna anotar el valor acumulado de ese porcentaje.
- Representar en una gráfica la curva resultante de los porcentajes acumulados de izquierda a derecha.
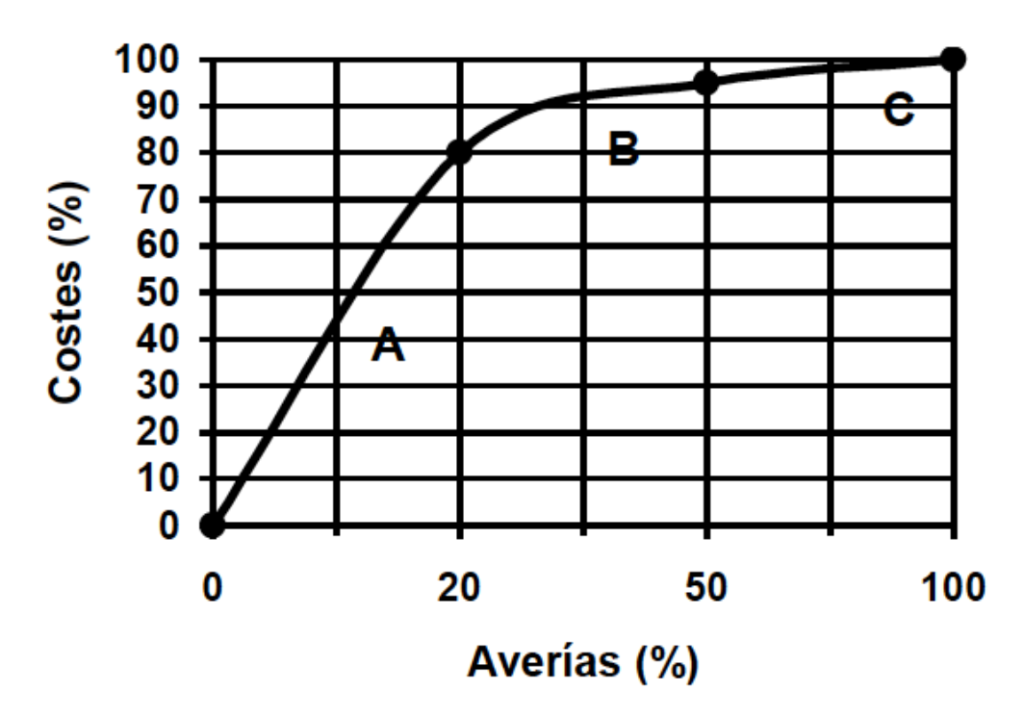
En la representación gráfica se pueden identificar tres zonas:
Zona A: En la mayoría de análisis se aplica el principio de pareto, el 20% de las averías causa el 80% de los costos de mantenimiento.
Zona B: Del 20% al 50% de los eventos de falla, es decir el 30% del total, se causan el 15% de los costos de mantenimiento correctivo.
Zona C: El 50% de los eventos de falla de un activo causa el 5% de los costos totales.
Análisis de Resultados
Con los resultados obtenidos gráficamente y en conjunto con los datos tabulados se pueden deducir las siguientes acciones a implementar en la gestión de mantenimiento del activo.
- Las fallas situadas en el área A, serán susceptibles de seguimiento estricto, implementando acciones de mantenimiento preventivo, manteniendo stocks de inventario de repuestos e insumos adecuados y calculados en conjunto con la tasa promedio de fallos MTBF y adicionalmente se recomienda correr un análisis RCA más profundo para detectar posibles fallas en cuanto diseño, instalación, condiciones de operación, calidad de piezas, mejora de aleaciones, protección eléctrica entre otras más acciones correctivas que se pueden implementar para reducir los costos ocasionados.
- Las fallas situadas en el área B, tienen una exigencia de esfuerzo menor en cuanto a carga de trabajo y costos y requerirán menores capacidades empresariales que se pueden trasladar a otros activos con igual o mayor criticidad.
- Las fallas situadas en el área C, requerirán mucho menos recursos, aunque la tasa de averías es mayor, esto podría ocasionar un incremento en la programación de ordenes de trabajo y se recomendaría implementar mejoras de ingeniería y optimización de los procedimientos de mantenimiento para reducir la carga laboral ocasionada por la frecuencia de las fallas menores.
Ejemplo de Aplicación
A continuación se puede apreciar el análisis de Pareto para un historial de fallas y sus costos en una bomba centrífuga con sello mecánico:
Historial de fallos en el equipo:
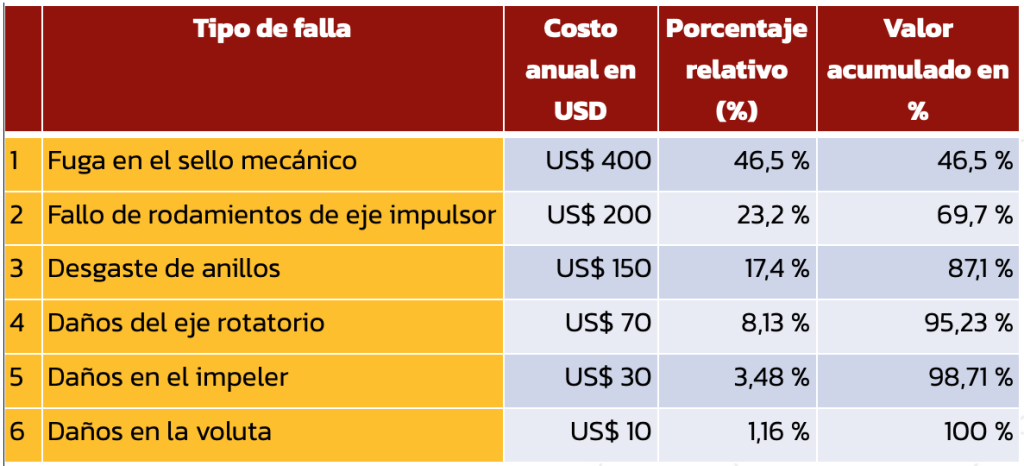
Posteriormente se lleva a un gráfico del número del tipo de falla versus el valor acumulado en %:
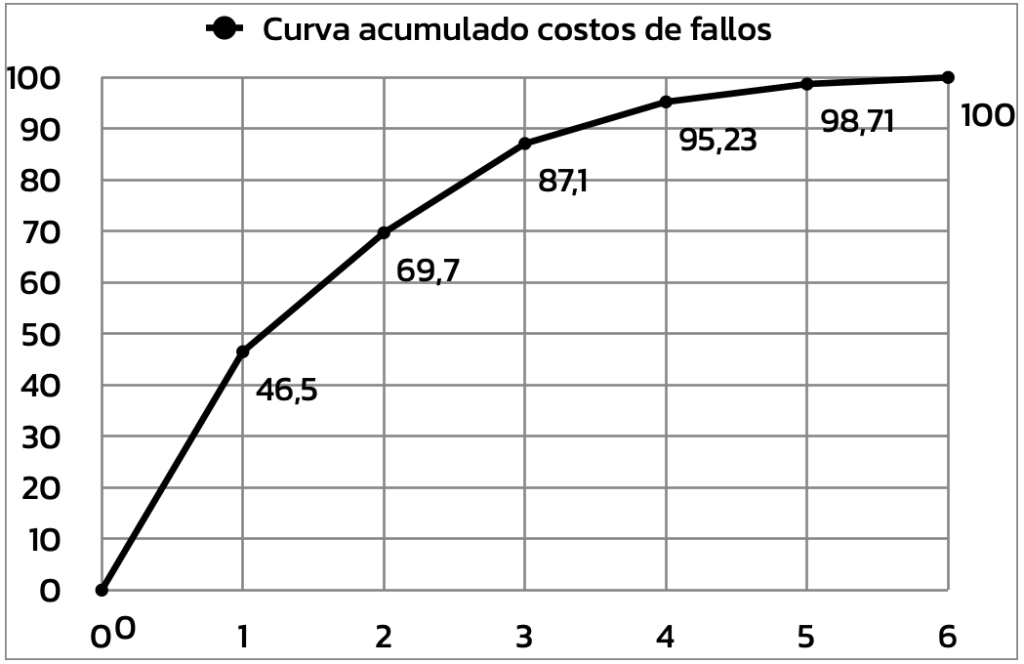
Se pueden realizar varios análisis de la curva de la gráfica tipo ABC obtenida, las fallas 1,2,3, falla en el sello mecánico, fallas en los rodamientos del impulsor y desgaste en los anillos respectivamente, corresponden al 87,1% de los costos de mantenimiento anual asociados a fallas de la bomba centrífuga, se pueden concluir varias situaciones que necesitan acción correctiva:
- El sello mecánico utilizado no es de buena calidad, lo barato sale caro a mediano plazo.
- El proceso de instalación del sello mecánico es incorrecto, puede que se haga torque o esfuerzo excesivo que causan micro-fracturas en el material del sello.
- La presión de operación de la bomba esta por encima de la presión de diseño (mantenimiento basado en condiciones).
- El fluido movido por la bomba es corrosivo o no es compatible con los materiales del sello mecánico, (ejemplo: diesel, soda cáustica).
- La presión de vapor del fluido esta por encima de la presión de operación causando la aparición de micro burbujas que chocan con todo el cuerpo interior de la bomba.
- El lubricante utilizado no es el recomendado para el funcionamiento de la bomba.
- Entra agua o fluido a la cámara donde se almacena el lubricante, causando su contaminación y nula o disminuida capacidad de lubricación.
- El lubricante no se reemplaza con la frecuencia adecuada.
- El eje de la bomba no esta alineado entre el motor eléctrico y el cuerpo giratorio.
- El fluido movido por la bomba es muy viscoso y la selección del equipo fue incorrecta basado en esta variable.
- La altura del fluido en el punto de succión ocasiona sobre presión en la bomba.
- Le entra aire a la bomba en algún punto.
- El diámetro del impeller no es el adecuado para el tamaño de la bomba.
- La temperatura el fluido es muy alta y afecta los mecanismos interiores de la bomba.
Se pueden seguir sacando muchas conclusiones acerca de las fallas que ha tenido el activo durante el año, a través de un análisis RCA, se determinarían las causas reales de las fallas 1, 2 y 3 y así se implementarían las acciones correctivas para reducir ese 87,1% de los costos.
Mediante un CMMS que permita programar a tiempo los mantenimientos preventivos y permita hacer una monitorización de parámetros como la temperatura y presión, el área de mantenimiento estaría en capacidad de anticipar fallos y en forma conjunta poder disminuir los costos y la carga de trabajo requerida por el activo.
Otros Puntos de Vista de Análisis Usando la Metodología de Pareto
La aplicación del principio de Pareto es muy versátil, se pueden analizar muchas variables en función de un mismo resultado: el análisis de falla, este es uno de los indicadores gerenciales más importantes ya que un estudio concienzudo de los resultados y la implementación de acciones correctivas trae muchos beneficios, únicamente aplicando el principio “Separar los pocos vitales de los muchos triviales”, resuelve mucho esfuerzo en la resolución de problemas.
Es posible hacer análisis diferentes, extractando la información de un CMMS (para más información de nuestro CMMShere consulta nuestro Ebook: Sistemas de gestión de mantenimiento computarizado) la frecuencia de fallas del activo, construyendo una gráfica con los acumulados en números de falla o en horas de falla por evento de mantenimiento correctivo, teniendo en cuenta los totales de uno o del otro, para un periodo analizado cualquiera:
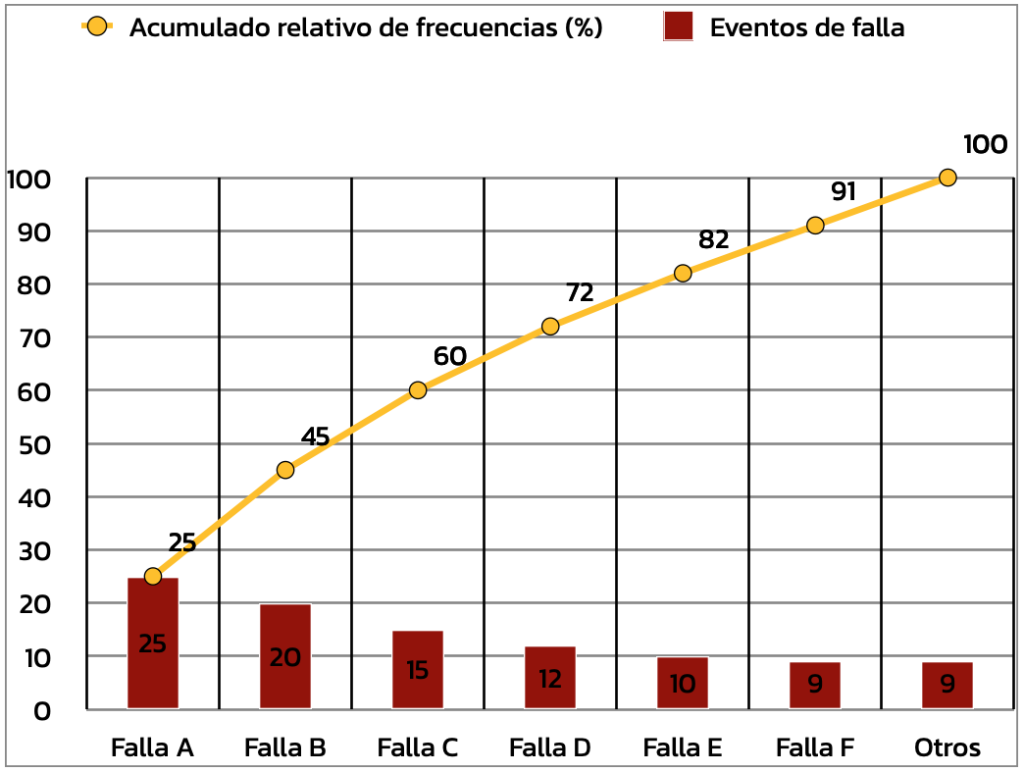
En este caso teórico, se puede apreciar que las fallas A,B,C,D y E contribuyen al 82% de la frecuencia total de fallas en el activo, por tanto se deben centralizar los esfuerzos a mitigar o a reducir la tasa de fallos mediante la implementación de acciones correctivas.
Se puede continuar realizando análisis gráficos por tipo de mantenimiento, como cantidad de mantenimiento preventivos por activo, cantidad de reparaciones o mantenimientos correctivos, monitorización de variables por condición, reparaciones por defectos, uso de determinado repuesto en activos, también la metodología es aplicable a análisis más profundos, tales como el modo de fallas de tipo eléctrico y en este se graficarían los sub tipos, como cortos eléctricos, desajustes, picos de corriente, factor de potencial entre otros.
Usos de la Metodología de Pareto
Gracias a su dinamismo y enfoque de separación de lo vital de lo trivial, se puede aplicar la metodología en varios campos:
- Identificación de puntos de mejora, cambios de diseño y optimización en la instalación de equipos.
- Evaluar los resultados obtenidos de la implementación de acciones correctivas, haciendo una paralelismo entre el antes y el después en un procedimiento de mantenimiento, proceso productivo o la prestación de un servicio de mantenimiento de equipos de terceros.
- Puede contribuir a los análisis de causa raíz como complemento del estudio de causa y efecto de eventos de falla.
- Analizar agrupaciones de datos que tienen un fin común.
- Mejorar la calidad de un producto o servicio al realizar análisis de PQR´s y encuestas de satisfacción.
- Es una herramienta de toma de decisiones y resolución de problemas para gerentes en lugar de estar en el modo de “apague de incendios”.
La Metodología de Pareto en CMMShere
Llevar el historial de fallas de un activo o de todos los activos de una organización en hojas de cálculo es dispendioso, poco preciso y nulo en tiempo real, nuestro CMMShere tiene las capacidades para aplicar esta metodología y obtener sus beneficios:
- CMMShere posee la capacidad de asignar fallas a activos, indicar cómo fue el método de detección de la falla, personalizar la clasificación de acuerdo a la codificación de fallas de la organización, asignar la causa aparente de la falla y su seriedad.
- El CMMShere tiene en cuenta si la falla ha causado la salida de operación de otros activos en la cadena de proceso y determina los tiempos de reparación.
- Puede accesar a un gráfico de fallas completo con toda la información para que se realice un análisis de Pareto en los periodos de tiempo objeto de estudio.
Para mayor información de nuestro CMMShere, puedes consultar:
Aún no hay comentarios, ¡añada su voz abajo!